Steel is the most recycled material in the world, and can be reused any number of times without it losing its intrinsic characteristics.
With our production cycle we provide an important example of a circular economy, as we produce steel from scrap, thereby avoiding its dispersal into the environment and reducing the consumption of natural raw materials (e.g. iron ore) to produce new steel.
The steel produced by Feralpi is 98,6% recycled material.
Waste and production scrap are mostly sent for recycling and/or classed as by-products with only some residual waste requiring disposal.
We don't stop at just minimising product waste, we also apply a wider vision which extends to reducing the movement of raw materials and waste, reducing disposals, and replacing raw materials.
The first step towards an ethical model is reducing the production of waste. To do this we organise and manage processes and plants to minimise volumes and monitor impact.
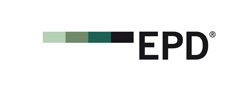
Life Cycle Assessment at Feralpi Siderurgica
Feralpi has implemented methods for evaluating the environmental impact of its products, using a life cycle assessment in accordance with standards ISO 14040 and ISO 14044. This method examines the phases of the product life cycle from the raw materials through to its release from the factory.
These assessments have made it possible to obtain the Environmental Product Declaration (EPD) in accordance with standards ISO 14025 and EN 15804, endorsed by independent third-party organisations for providing verified information on the environmental footprint relating to products.
In addition to the EPD, Feralpi has also carried out carbon footprint studies for products (CFP) made by Feralpi Siderurgica, Acciaierie di Calvisano, Presider, Caleotto and ESF Elbe-Stahlwerke Feralpi GmbH, endorsing them through standard ISO 14067. The EPD and CFP are tools that provide an overall evaluation of environmental impact, making it possible to communicate product environmental performance with transparency and obtain a market competitive edge. These tools also enable Scope 3 emissions to be studied, identifying areas along the production chain that require action. All studies have been checked by external bodies with a reputation for guaranteeing accurate, reliable results.
On our path-to-zero waste, we have set up the SteelZeroWaste project to lay the foundations for eliminating all production waste, and implementing innovative solutions to reduce environmental impact.
We are aiming for a total reduction in waste by reducing CO2 emissions (through capture and reuse), eliminating solid waste from the production cycle (and reuse as by-products for the internal cycle and external use). We promote the use of by-products made of plastic and encourage the reduction of plastics in the environment.
-
Black and White Slag
The recovery of black and white slag and the related operations are entrusted to external companies who also handle the trading operations. At the Lonato del Garda premises black slag is turned into the commercial product known as Greenstone, marked as CE 2+ and used in the construction industry to replace natural materials. It comes with an Environmental Product Declaration (EPD). Black slag is also recovered at the Calvisano premises to produce certified CE 2+ products. FERALPI STAHL has started the operations required to create reuse conditions for white slag at the Riesa facility, as is the case at the Lonato del Garda site.
-
Heat
The Feralpi Siderurgica premises in Lonato del Garda and the FERALPI STAHL factory in Riesa recover heat from cooling water and the smelting furnace in the steelworks, respectively. The Feralpi Siderurgica plant heats the buildings on the premises and, thanks to collaboration with the local council, public and private buildings in the council area are also heated. The plant at ESF Elbe-Stahlwerke Feralpi GmbH produces up to 30 t/h of steam, which is partly conveyed directly from the local municipal enterprise in Riesa (Stadtwerke Riesa - SWR) to Goodyear Dunlop Tyres and partly used to generate electricity. Residual heat from compressor stations is used to warm water and provide it for the technical administration offices in Riesa.
In 2023 a district heating project commenced at the Arlenico site, involving the implementation of a heat production plant by recovering waste heat from the rolling mill production process and a second setup in the area of SILEA in Valmadrera, where heat is recovered through a waste-to-energy system, capitalising on the heat generated from the plant that is currently released to the atmosphere.
-
Refractory material
Spent refractory materials from ladle demolition are reintroduced into the production cycle as partial substitutes for raw materials.
The raw materials to be replaced consist of calcium lime and dolomitic lime ("CaO lumps" and "CaO 40%") which are used in the Electric Arc Furnace (EAF) as fluxing agents. Their reuse in the furnace does not have any negative impact on the environment or human health.
-
Dust and Off gases
Recovery of dust and flue gases to reduce the demand for zinc
Fume abatement dust from the smelting process is mainly recovered by external plants and constitutes the zinc metal component, replacing that which comes from the natural mineral. Dust produced from the iron alloy plant is returned directly to the production cycle, with use equivalent to that of the materials that produce it.
-
Non-ferrous metals
Recovery of non-ferrous metals from scrap sorting.
The residual fraction resulting from the scrap sorting plant is sent to external plants for recovery by mechanically sorting non-ferrous metals such as aluminium, brass and copper.
-
Mill Scale
Recovery of mill scale to replace iron ore in the construction industry.
Mill scale is sent for recovery for external use. Green iron is the by-product from mill scale which is sold to plants for the production of counterweights and cement.
-
Sludge
The Feralpi Siderurgica facility in Lonato has a new sludge filtration plant, enabling the production of less humid residue which is therefore more suitable for recovery in a construction setting.
In this circular economy scenario, collaboration with stakeholders in the supply chain, and private, public and external stakeholders is strategic.
Some of our partners who have been joining us in the development of circular solutions over the years include Enea, Rina, Brescia University, Tenova, Di.ma, I.Blu, Energard, Agroittica, Italghisa, Tecnoproject and Biosyntesy.